The world’s longest EN156 polyurethane wind turbine blade cooperated by Times New Materials (TMT) Envision will be produced in small batch.
The trial production of this blade started in early March 2021. The spar web, spar cap and shell are all made of new polyurethane resin. Compared with traditional epoxy resin, polyurethane resin has better mechanical properties and fatigue resistance, faster infusion and curing speed, good processing performance, low volatile organic compounds and relatively favorable price.
Under the background of the rising price of epoxy resin in 2021 and the cost reduction and efficiency increase of the whole wind power industry, the cost advantage of polyurethane has also been highlighted.
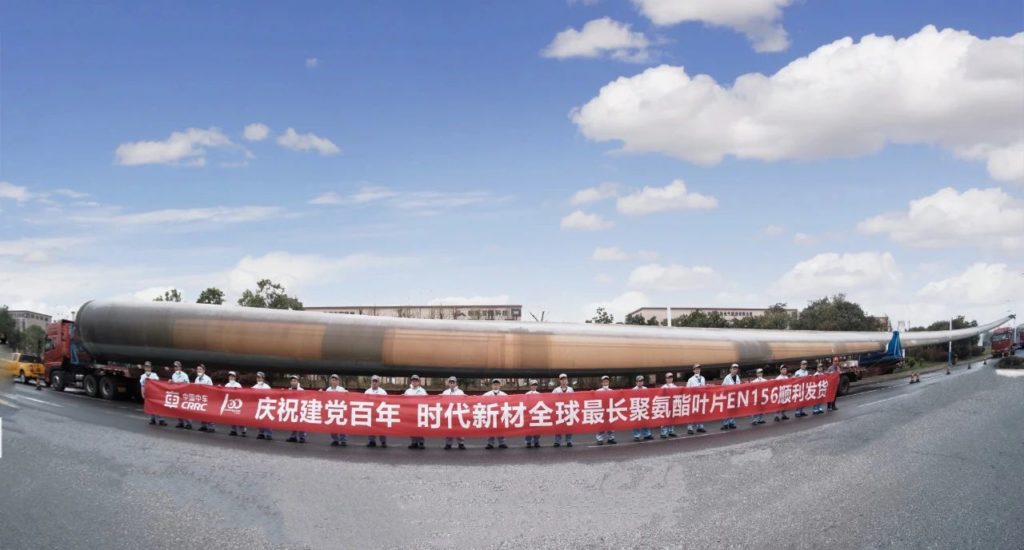
In addition to EN156, polyurethane has been used in other four types of blades by TMT. TMT is the only Chinese enterprise with batch manufacturing technology and ability of polyurethane blade. As early as 2018, TMT used polyurethane resin for blade production for the first time in China. The introduction process of polyurethane resin for large components was systematically studied, which solved the problems of polyester resin sensitive to humidity, fast reaction and short application period. The multi function and multi process integrated on-line vacuum infusion equipment was creatively developed to form the “mixing and injection” liquid-phase forming technology. The automatic control of key process parameters such as pressure, temperature and flow rate in the infusion process was realized, and the infusion efficiency and product quality were improved. Under the premise of equal stiffness, the resin absorbing capacity of glass fiber is reduced to further realize blade mass reduction.
The 2. XMW wind turbine blades with new high-performance polyurethane resin system independently developed by TMT in 2018 have passed the three-year on-line assessment, and the blades operate in good shape.
Source: TMT
Edited and translated: minds:connected