Future rotor blades will be larger than ever before. At the same time, there is a very strong pressure to make the next generation of rotor blades lighter and cheaper than ever before.
The following graph shows the blade mass in relation to the blade root bending moment over time of design. Each dot represents a WINDnovation design. The color of the dots indicate the length of the blade. It can be seen that there is a strong trend towards a mass reduction in relation to the blade root bending moment. This means that the recent blades utilize the materials higher than ever before and approaching the design limits of the blades closer than ever before.
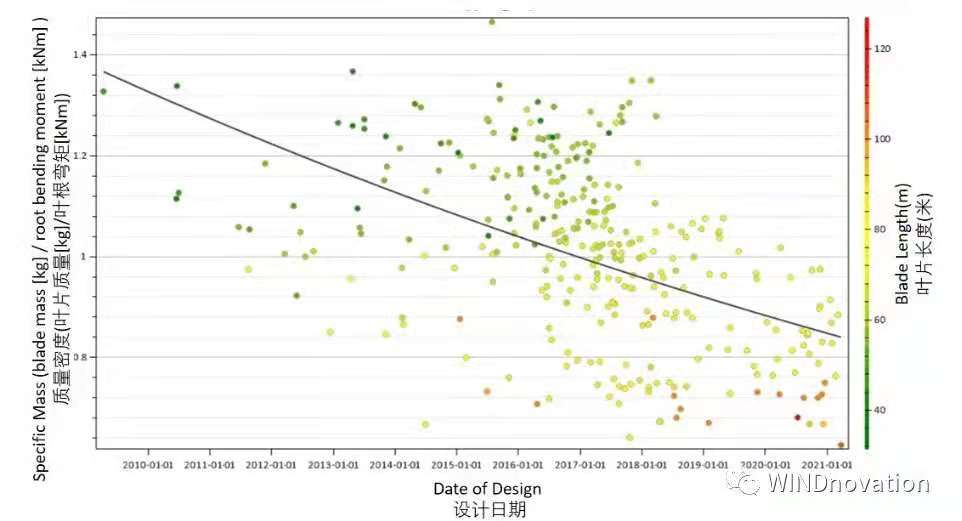
For the design engineers this trend means that the safety margins from the materials properties and the design calculations are getting smaller and smaller and the verification of the blades by full scale testing (static and fatigue) is getting more and more important.
At the same time, the increasing size of the blades unavoidably lowers their natural frequencies and the time for testing 1 million cycles flapwise and 2 million cycles edgewise in resonance mode is getting longer in proportion to the lower natural frequencies.
Furthermore, the more and more wind turbine specific derivatives of one base model of a rotor blade are designed which – following the certification strategy strictly – would need their individual tests. In most cases, this is not economic reasonable due to the high cost involved and the time needed.
A quite popular workaround is to specify so called “Synergy Tests” which combine different blade structures and different load sets the individual blades have to stand. It is easy to imagine that the cost and time advantage of such Synergy Tests is not for free. In most cases, the blade which undergoes the Synergy Test is a conservative combination of the different blade structures and – even worse – needs further structural modifications to stand the test loads coming from an envelope over the different load sets. To use a simplified wording, the blade tested is reinforced to stand the combined test loads and is consequently heavier than any serial blade it represents. As most of such reinforcements can not be removed for the serial blades, all serial blades show a weight penalty due to the test procedure applied.
A third mostly necessary but unfavorable item is that the blade undergoing the fatigue test has to be equipped with heavy devices for frequency excitation (eg. cycling masses) and single point masses to move frequencies, which change the properties of the blade to be tested.
WINDnovation as the leading rotor blade designer has teamed up with Shanghai Zhongzhen Technologies known in China as a leading designer of test equipment for rotor blades to address these issues:
- Local overloading of the blade due to load introduction shall be avoided
- Design of an over-weight blade “just” to stand the test loads shall be avoided
- The test equipment shall avoid to attach any local point masses to the blade
- Instead of performing the flapwise and edgewise fatigue test one after the other, they shall be performed simultaneously
The solution which is currently under development, is to use (instead of shakers or linear moving masses installed on the blade) rope based actuators only. The ropes shall be applied at multiple positions of the blade and in flapwise and edgewise directions simultaneously. The set-up is called the “Tug-System”. It is obvious, that the engineers for blade design, test specifications and test performance have to cooperate very closely.
During the next months, the Tug-System will be verified firstly by using it in flapwise and edgewise direction separately, and later in summer 2021 by combining the directions to a simultaneous test.
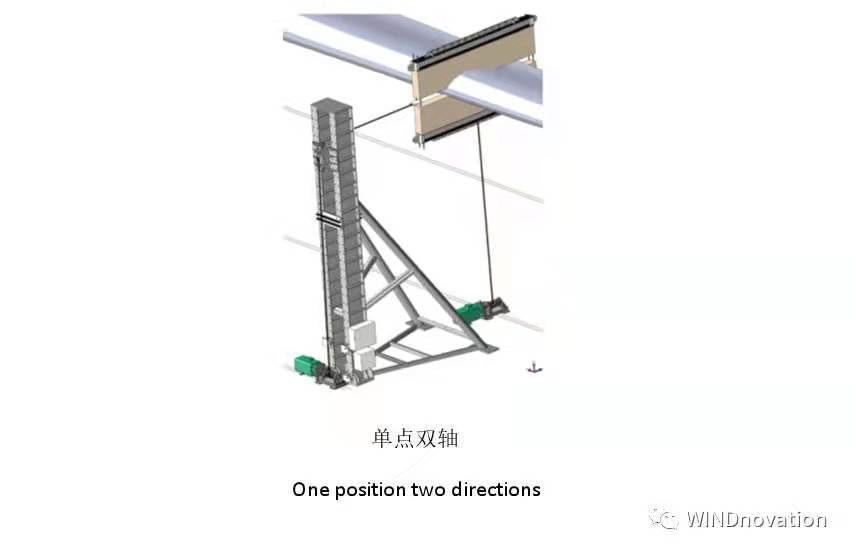
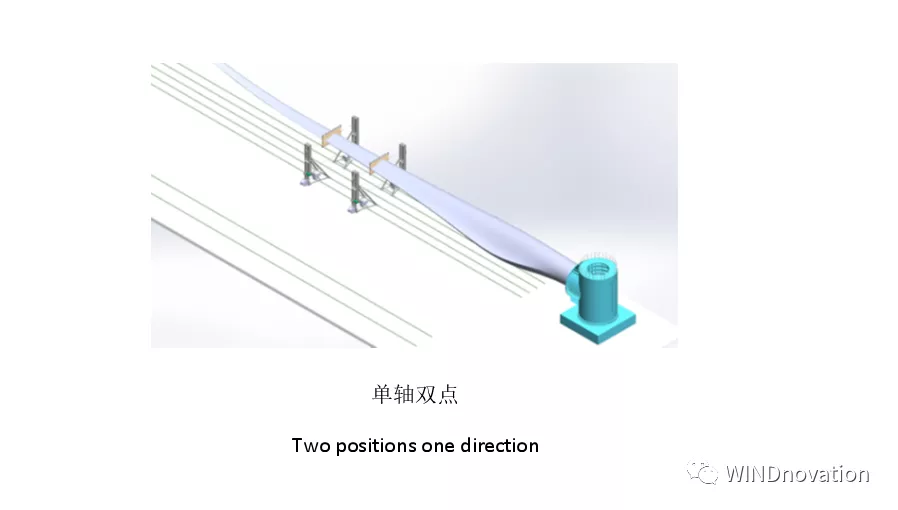
The system has been granted a Utility model in China already and an application in Europe is currently on the way.
The Tug-system is currently reviewed by UL and an approval that the system is in full compliance with the guidelines for testing of rotor blades is expected shortly.
Source: WINDnovation